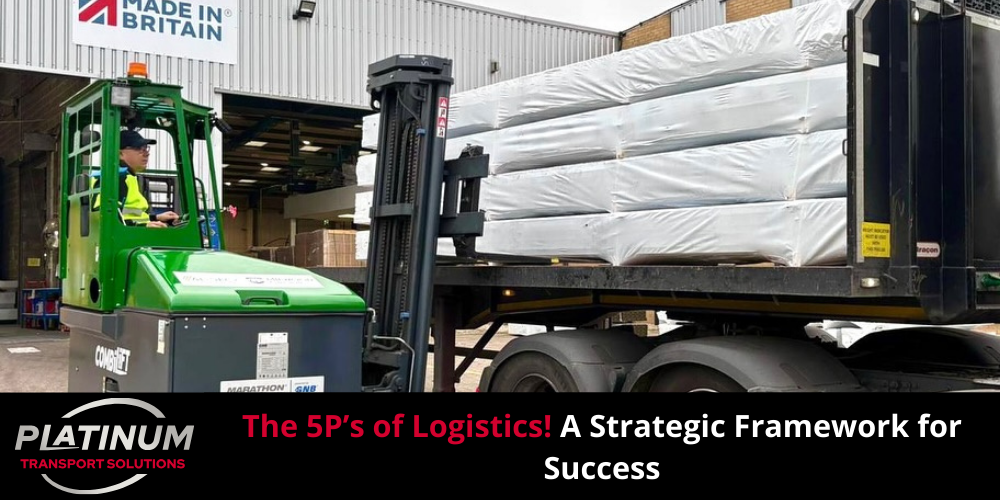
The 5 P’s of Logistics: A Strategic Framework for Success
In today’s fast-paced environment, effective logistics management is essential for staying competitive. Forward thinking businesses like Platinum Transport Solutions understand the value of using a clear, structured approach to focus on key elements that drive success. One practical strategy is the “5 P’s of Logistics,” a framework designed to streamline operations, improve efficiency, and ultimately boost outcomes. Each of the five components contributes towards creating an agile framework capable of improving warehouse logistics operations such as transportation or supply chain processes.
What are the 5 P’s of Logistics?
- People
- Products
- Processes
- Partnerships
- Performance
Let’s look at how these five pillars provide a pathway toward successful logistics in supply chains, helping companies meet operational challenges efficiently while meeting customer demands with agility and precision.
People: The Core of Logistics Operations
At the core of logistics operations are skilled and motivated professionals. Roles like warehouse managers and supply chain analysts are crucial in inventory control and transportation planning functions. Furthermore, investing in workforce training helps teams proactively address unexpected issues before they arise. Promoting team communication and collaboration streamlines coordination and reduces bottlenecks, ensuring smooth operations.
Tips for Fostering a Strong Logistics Team:
- Provide ongoing training in logistics best practices.
- Encourage collaboration between departments to improve process flow.
- Recognise and reward employee contributions to boost morale and motivation.
Products: The Focus of Transportation
Logistics services aim to transport products between two locations efficiently. Understanding the unique handling, storage, and transport needs of different products is paramount for efficient logistics management; for instance, frozen foods require cold chain logistics, while high-value electronics require secure packaging solutions tailored specifically for them. By customising solutions around specific requirements for optimal product arrivals, logistics teams ensure customer satisfaction while simultaneously increasing company profits.
Considerations for Product-Centric Logistics:
- Use appropriate packaging materials to prevent damage.
- Implement temperature-controlled logistics for perishable goods.
- Regularly audit warehouse logistics processes to ensure products are stored according to specifications.
Processes: The Blueprint for Efficiency
Logistics processes rely heavily on efficient methods for smooth movement, storage, and tracking of goods. Optimising order picking, packaging, and shipping processes can significantly enhance efficiency while cutting costs and errors.
Analysing each step in the supply chain to identify redundancies or inefficiencies helps identify areas that need fixing. At the same time, automation, such as real-time tracking, minimises manual tasks while streamlining operations.
Finally, having a standardised workflow enables logistics teams to respond when faced with both expected and unexpected challenges, increasing overall efficiency.
Critical Steps for Streamlining Logistics Processes:
- Map out the logistics workflow to identify potential bottlenecks.
- Incorporate technology solutions for automation and real-time tracking.
- Continuously evaluate and adjust processes based on feedback and performance data.
Partnerships: Building Strong Collaborative Networks
Logistics operations rely on strong partnerships among suppliers, transportation companies, and warehouse providers for effective collaboration and resource sharing. Such collaboration allows organisations to access external expertise while sharing resources across the supply chain. Trust and open dialogue help ensure successful partnerships, which enable logistics managers to negotiate better rates while increasing service levels and operational flexibility quickly.
Tips for Building Successful Logistics Partnerships:
- Select partners with compatible values and operational standards.
- Develop clear service-level agreements (SLAs) to outline expectations.
- Schedule regular meetings to review performance and address issues collaboratively.
Performance: Measuring Success in Logistics
Performance metrics are indispensable tools for analysing logistics operations and driving improvements. By monitoring key performance indicators (KPIs) like on-time delivery rates, order accuracy rates, transportation costs, and logistics, the logistics manager can identify areas for enhancement and alter their strategies accordingly.
Utilising data-driven insights allows businesses to adapt quickly to market changes while eliminating operations inefficiencies resulting from resource allocation inefficiencies or operating inefficiently. Performance metrics support customer-oriented logistics strategies by ensuring services align with customer expectations.
Essential KPIs for Logistics Performance Management:
- On-Time Delivery Rate – Measures the reliability of delivery schedules.
- Order Accuracy Rate – Assesses the precision of order fulfillment.
- Transportation Cost per Mile/Kilometer – Tracks the cost-effectiveness of transportation.
- Customer Satisfaction Score – Gauges customer approval and feedback.
Conclusion
The 5 P’s of Logistics provide a practical framework for effective logistics management. Each element is integral to creating an effective, resilient operation to meet fast-paced market demands. By prioritising them, companies can increase warehouse, transportation, and logistics efficiency and quickly meet customer requirements while strengthening organisational success.
Implementing the 5 P’s ensures your teams meet customer requirements while improving the company’s operational performance and reinforcing leadership roles within the logistics/supply chain sectors.